A Win-Win Situation
Apprenticeship program helps STIHL develop a skilled manufacturing workforce
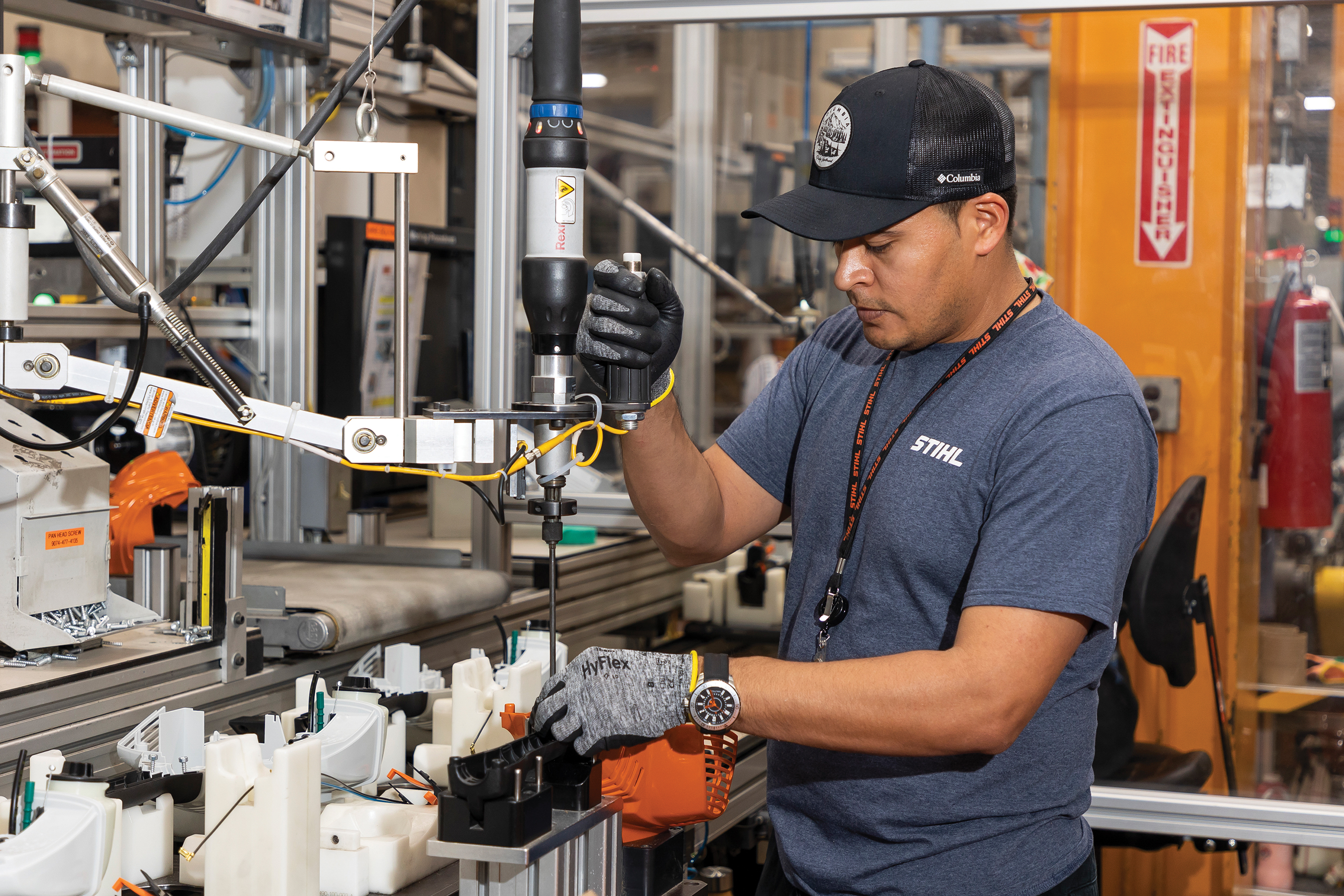
STIHL Inc., Virginia Beach
When Ryan Buzzy was a child, his passion was to take radios apart to see how they worked.
At 25, he’s not a kid anymore, but his passion for seeing how things work never changed. That’s why, eight years ago — less than two months after graduating from high school — he signed on to be an apprentice (and ultimately, an engineering technician) with German-owned power tool manufacturing giant STIHL Inc.
Buzzy started at under $50,000 per year, but has just about doubled his salary. As he put it, “Financially, it’s like I’ve been launched a decade into the future.”
The program that got him in the door at STIHL was created with an eye toward the company’s own financial future. Forty years ago, the company underwrote a unique domestic apprenticeship program that has since trained and hired nearly 70 young apprentices, with a remarkable 93% retention rate.
A New, Old Method of Workforce Training
A growing number of employers nationwide — some, perhaps, influenced by the eye-popping success of Virginia employers like STIHL — are waking up to the value of well-resourced apprenticeship programs. There are currently 600,000 registered apprentices of all kinds in the United States, a 106% increase from 10 years ago, according to the U.S. Department of Labor.
At the outset, the hard part is convincing college-minded parents — even more than their kids — about the potential benefits of apprenticeships, says Courtney Addison, manager of talent development at STIHL.
“In the U.S., there’s more of an emphasis on the college route after high school, and college gets pushed down a lot of kids’ throats,” she said. “But now, some students and parents are starting to look at other alternatives.”
One such alternative is STIHL’s apprenticeship program, which gets about 300 applicants annually and ultimately trains and hires an average of four every year. It’s not cheap. STIHL estimates it spent more than $1 million in all facets of training and development at the company last year, including for this program. But the payoff for the company is huge.
“Our goal is to select the best candidates for the program so we can train them to our level and our standards,” Addison said. “This creates a pipeline of talent for hard-to-fill positions,” including very specialized jobs like tool and die makers and polymer technicians.
Training an Employee, Molding a Person
Depending on the specific apprenticeship, the domestic program lasts from two-and-a-half to four years and includes a college education — fully paid for upfront by STIHL — at Tidewater Community College (TCC). Other employee benefits include health and dental insurance, paid vacation time, a 401(k) plan, and a company pension.
The process can be grueling. After an eight- to 12-hour day at work, apprentices are often expected to attend evening classes at TCC for up to four additional hours some evenings.
“The apprenticeship program is a huge commitment for students and their families,” Addison said, “but it’s worth it.”
Just ask Buzzy.
“If I step back and look at what I’ve accomplished in the past seven years, I’m so grateful for all the hard work I put into it,” he said. “If you work hard, you set yourself up to do well for yourself inside the company and outside the company.”
I had an opportunity to jump-start my life and live it the way I want to.
Buzzy has friends his age who went directly to college from high school and now have onerous student loan debt that has prevented them from buying new cars. In his case, as he put it, “I had an opportunity to jump-start my life and live it the way I want to.”
It all started at age 18, when it came time to take the Scholastic Aptitude Test if he wanted to go to college. “I didn’t really want to study for the SAT anyway,” he said.
During high school, he’d attended some tech classes at the Advanced Technology Center at TCC’s Virginia Beach campus. That’s how he found out about the STIHL apprenticeship program.
Learning a Career
The program starts with an eight-month “boot camp” to establish a baseline for apprentices, where they’re trained on basic safety issues so they can always operate safely on the floor. That was where Buzzy first learned to shape metal with specialized machines.
Next, apprentices go into rotations that include working in a variety of departments and attending night classes. On days that involve night classes at TCC, their days can stretch up to 16 hours.
Apprentices start out mostly observing experienced technicians, often former apprentices themselves, followed by a period of working with tools under close observation. Ultimately, apprentices get to work on their own.
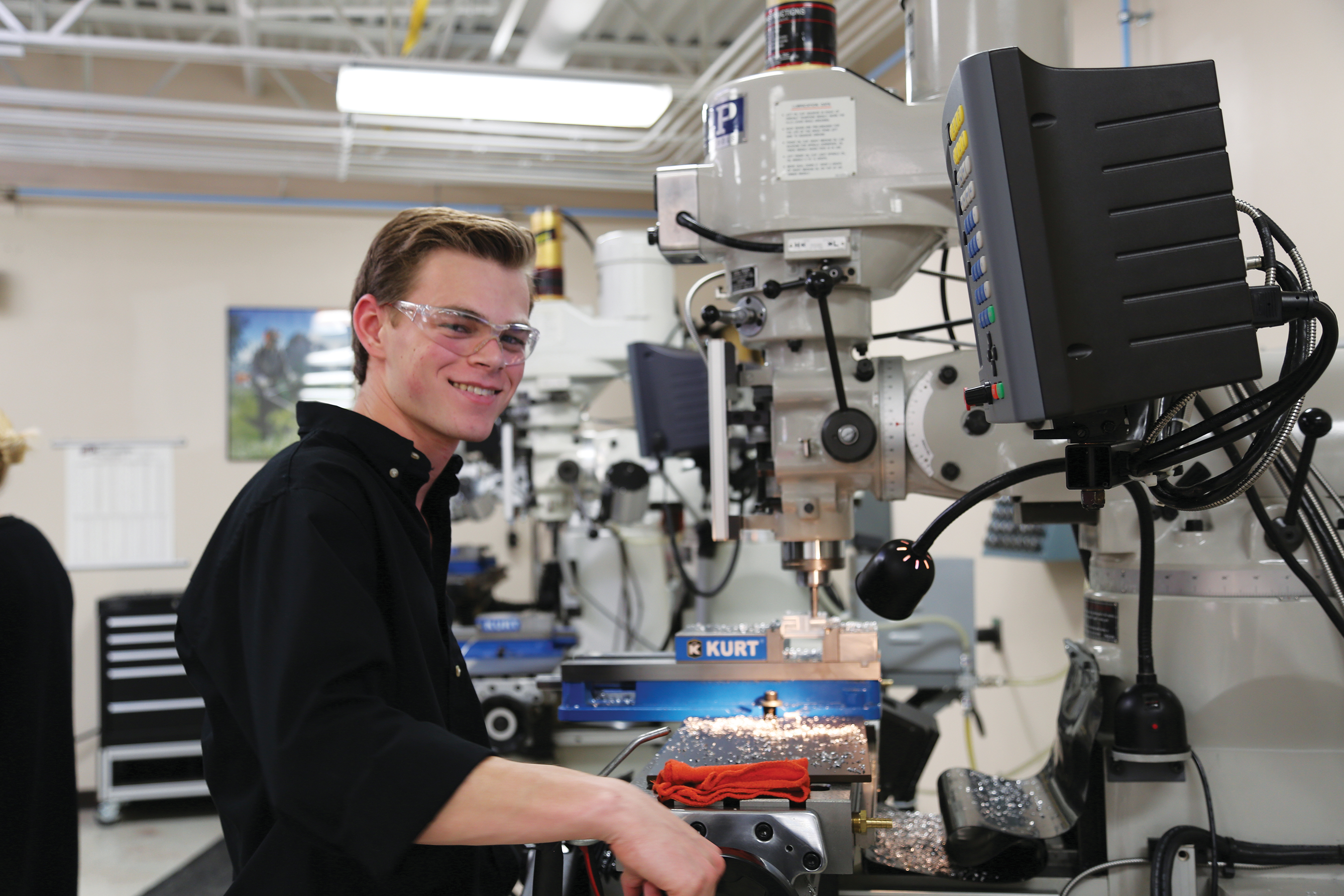
STIHL Inc., Virginia Beach
Over the initial two-year period, Buzzy mostly worked in the assembly maintenance department, learning about the assembly of the hundreds of parts that make up the power tools. This is where materials are put together for the trimmers, blowers, or chainsaws sold to consumers.
These long days did not bother Buzzy. In fact, he says, they gave him incentive to keep pushing harder. He stuck with the program for four years before graduating and joined the process engineering team at 22.
He’d already earned an associate degree in mechatronics, which combines the study of mechanics, electronics, and computer engineering — totally paid for by STIHL. He also earned a Virginia journeyman’s certificate.
His accomplishments at STIHL have been considerable. During the COVID-19 pandemic, he helped to design and assemble safety platforms that kept assembly line workers safe distances from each other. He’s even built full machine automations on his own.
“It’s like the adult erector set world,” he jokes.
Buzzy fully realizes that the opportunity is there to ultimately become an executive at STIHL. But at 25, he says, he’s still considering his options.
Taking Charge of Talent Development
Attracting workers with skills like Buzzy’s isn’t easy. The toughest thing for manufacturing companies like STIHL is recruitment, Addison said, because of stereotypes around the industry.
Meanwhile, the specialized trade skills required at STIHL are getting harder to come by. That’s why an apprenticeship program that trains from scratch is so critical to the company’s future.
“These skills are disappearing in Virginia and everywhere,” Addison said. “So we have to be proactive in creating and keeping the skillsets.”
For Buzzy, it’s been a long, steady climb since his childhood, when he first began tinkering with tractors and other farm machinery on his grandfather’s hobby farm.
“Every time I get good at something, I feel like I need to learn something else,” he said. “My goal is to keep learning. More than anything else, my apprenticeship taught me how to learn.”