A Biopharma Booster
Booming Virginia clusters provide a supply chain blueprint for increasing drug accessibility, affordability
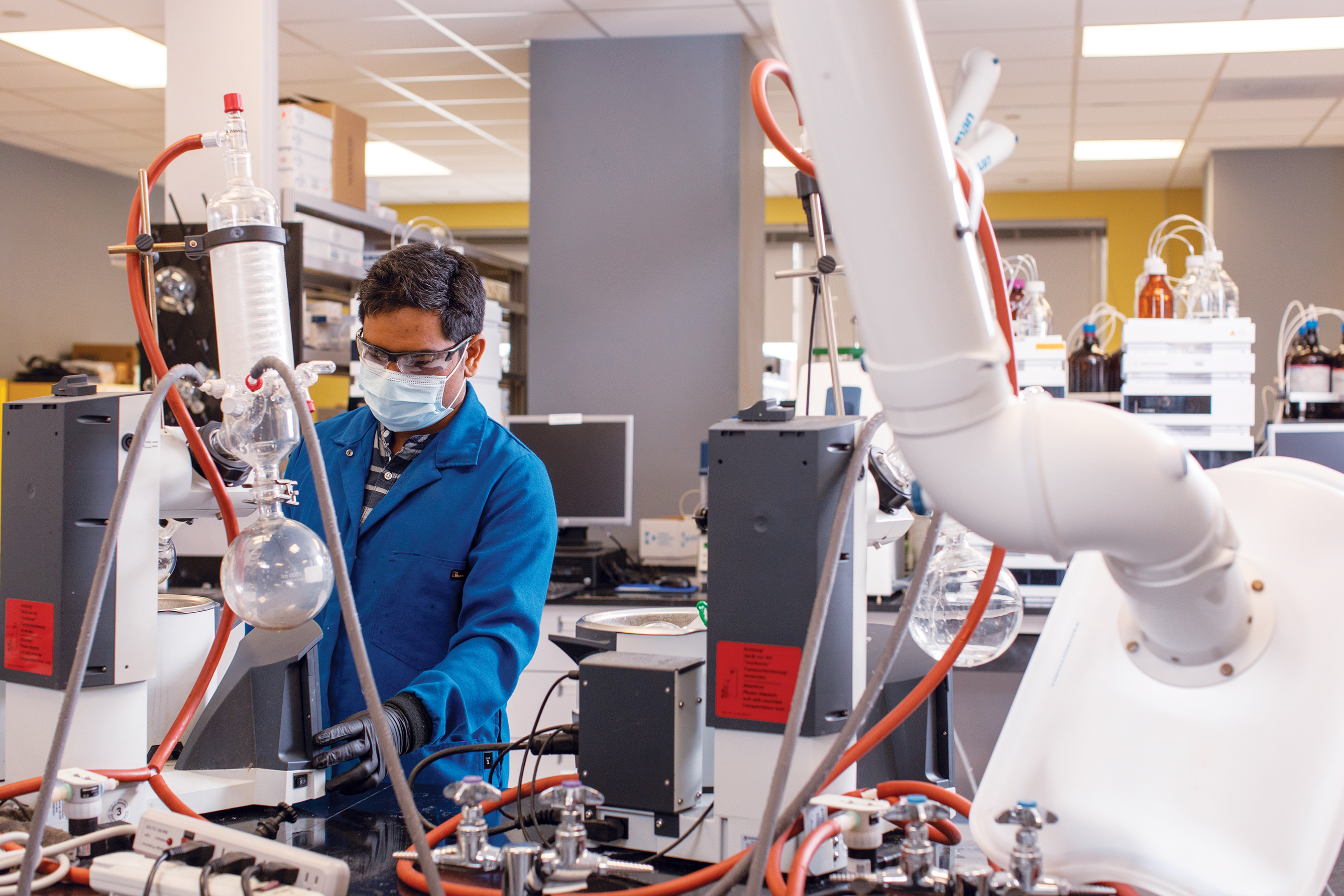
The Medicines for All Institute at Virginia Commonwealth University focuses on optimizing medicine production through innovative manufacturing techniques.
Like his fellow Type 1 diabetics, Alec Smith took insulin every day to regulate his blood sugar. Costs to treat his condition topped $1,000 per month, most of that going to insulin, and Alec made the difficult decision to ration his insulin to save money after aging off his mother’s health insurance plan.
Rationing insulin is a delicate process for diabetics. The body’s insulin needs can fluctuate significantly due to changes in diet, exercise, stress, poor sleep, or other medications, and diabetics must constantly monitor their glucose levels even when taking insulin as directed. When a person’s blood sugar gets too high, the body goes into diabetic ketoacidosis, which releases dangerous amounts of acid into the bloodstream and, if left untreated, can result in death — as it unfortunately did for Alec Smith in 2017. His mother, Nicole Smith-Holt, told CBS News, “I think if the price of insulin in 2017 had been $35, Alec would still be alive today.”
Alec was not alone. A 2022 study from the Annals of Internal Medicine found that one in six Americans who take insulin have rationed their dosage due to cost concerns. Some brands of insulin have been in shortage multiple times since 2023, leading to congressional inquiries of major insulin producers in the country. Nearly 30 million Americans have diagnosed diabetes (Type 1 or Type 2), and more than 7 million require daily insulin.
The problem isn’t limited to insulin. Across the U.S. biopharma industry, supply chain gaps and delays and impaired coordination have led to rising consumer costs and mounting shortages. The American Society of Health-System Pharmacists counts more than 200 U.S. drug shortages, with critical medications used to treat cancer as well as sterile injectables and generic drugs among the deficiencies.
“Make no mistake, drug shortages are not a passing storm that will soon blow over,” said Allan Coukell, senior vice president of public policy for pharmaceutical manufacturer Civica Rx, during a 2023 congressional hearing. “After a dozen years, shortages must now be understood as a built-in and permanent outcome of our current system.”
Civica, a nonprofit generic drug company with a growing presence in the central Virginia cities of Richmond and Petersburg, is one of an increasing number of forward-thinking Virginia companies focused on making medicine like insulin more accessible — targeting shortages while making biopharmaceuticals more affordable for consumers. Across Virginia, innovation and collaboration have transformed the Commonwealth into a thriving ecosystem that’s making a difference nationally.
A Biopharma Sweet Spot in Central Virginia
The lessons learned from the COVID-19 pandemic were seemingly written in invisible ink. Instead of strategically stockpiling critical medicines, many U.S. manufacturers have reverted to a “just-in-time” approach, and many critical drugs and ingredients are manufactured overseas.
But over that same period, Virginia — and the Richmond-Petersburg region in particular — has emerged as a model for biopharma companies seeking to put much-needed medicines in the hands of consumers faster and cheaper.
“There really is no place in the nation this focused on advanced manufacturing,” said Robby Demeria, chief corporate affairs officer for Phlow Corp., a Richmond-based Certified B Corporation with a manufacturing facility in Petersburg. “There is significant activity. Stars are aligning.”
There really is no place in the nation right now this focused on advanced manufacturing. There is significant activity. Stars are aligning.
Phlow is focused on leveraging advanced manufacturing processes to re-image the domestic production of key starting materials and active pharmaceutical ingredients (API), an area of particular vulnerability for the United States.
In 2024, the Active Pharmaceutical Ingredient Innovation Center, a consortium of biotechology industry leaders, found that more than 90% of the most frequently prescribed antivirals and antibiotics have no domestic API manufacturing source. Phlow has a close affiliation with another altruistic biopharma organization, the Medicines for All Institute (M4ALL) at Virginia Commonwealth University’s (VCU) College of Engineering.
Launched in 2017 with funding from the Bill & Melinda Gates Foundation, M4ALL is committed to innovating efficient manufacturing processes, including API production as a means of creating more access and affordability.
“It starts with chemistry,” said Dr. Frank Gupton, M4ALL’s CEO. “If we have robust, high-yield chemical processes, then we can do a lot of things with the downstream steps and greatly simplify the processes.”
With that approach, M4ALL has led improvements to more than 20 drugs for COVID-19, HIV, tuberculosis, and malaria.
That brings us back to Civica, the nonprofit that’s currently delivering 80-plus drugs directly to member hospital systems across the country. In 2022, Civica struck an agreement with GeneSys Biologics to manufacture and distribute three insulins at significantly lower prices than those currently available in the United States, sold at a recommended price of no more than $30 per vial and $55 for a box of five pen cartridges. The company’s new Petersburg facility has the capacity to produce about 90 million vials and 50 million prefilled syringes per year.
Rounding out the Richmond-Petersburg cluster are AMPAC Fine Chemicals (AFC), a division of SK pharmteco that manufactures custom API and registered intermediates, and United States Pharmacopeia (USP), an independent scientific nonprofit that establishes quality, purity, and other standards.
The cluster is a highly coordinated, streamlined ecosystem capable of true turnkey manufacturing. In 2021, Civica announced plans to build a 140,000-sq.-ft., $140 million manufacturing facility in Petersburg. With support from this strategic partnership led by Phlow, Civica’s cutting-edge facility was designed for the manufacture of sterile injectables — converting AFC and Phlow’s API into finished medications. Soon after that announcement, AFC broke the news of its own $25 million expansion.
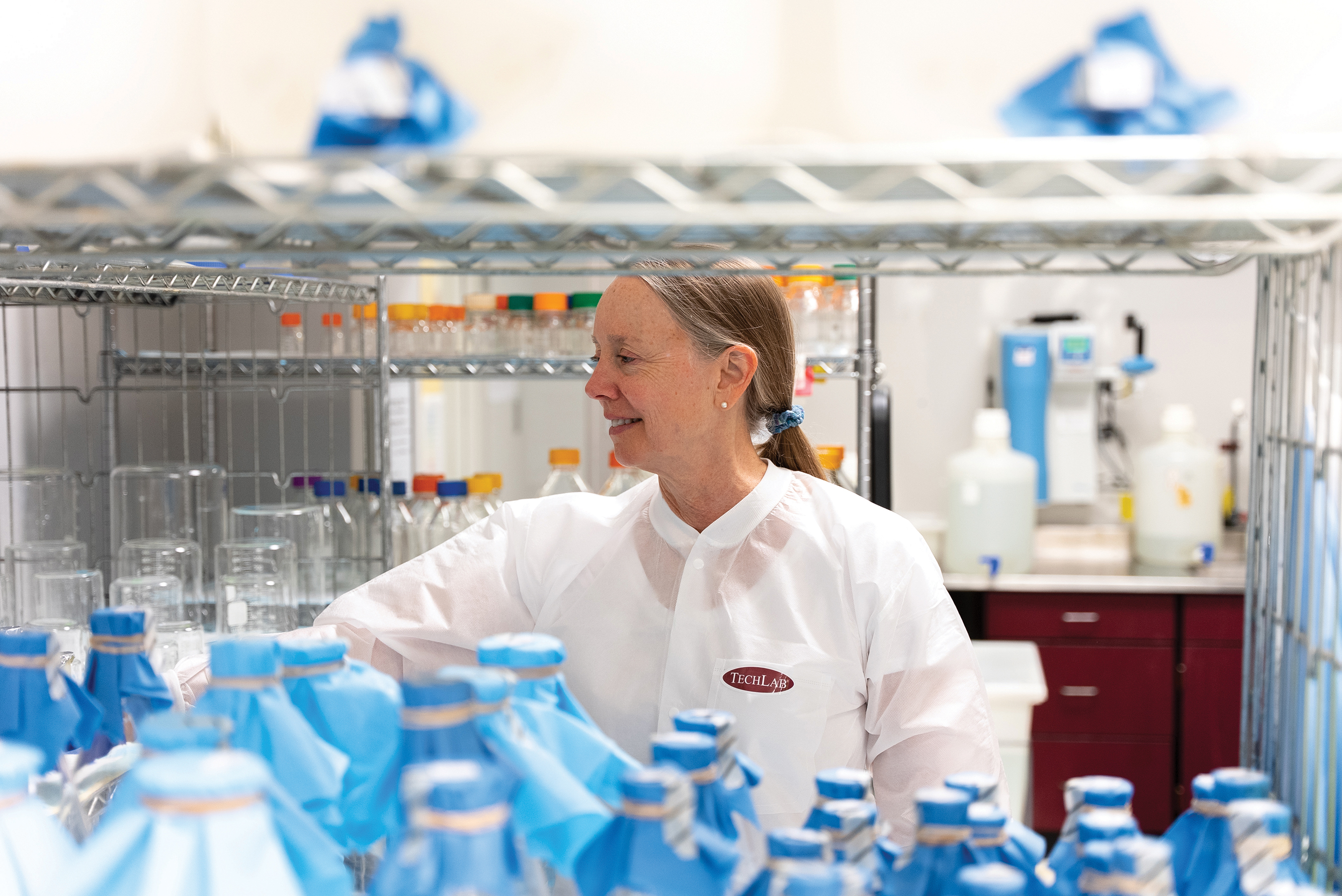
Founded by Virginia Tech researchers who were investigating diagnosis and treatments for major hospital pathogens, TECHLAB, Inc., designs, develops, and manufactures infectious disease diagnostics that are distributed worldwide.
Rewriting the Map
Plot out the trade routes illustrating a medication’s journey from manufacturing facilities to a U.S. patient’s medicine cabinet, and you’ll see lots of activity flowing from East to West.
It’s not only the API that largely comes from Asia, but also the critical final step of the biopharma manufacturing process: fill-finish. This step involves dispensing the medication into a syringe or vial, as well as any needed sterilization and other final touches.
According to Demeria, the volume of generic essential medicine fill-finish work completed in the United States just recently dipped below 50%, with much of it occurring in India.
Central Virginia’s biopharma cluster is looking to not only bring these key functions stateside, but also to shore up the supply chain by building the U.S. stockpile. To that end, Phlow has partnered with the U.S. government to add millions of doses of essential medicines to the Strategic National Stockpile, aided by a $354 million contract from the U.S. Biomedical Advanced Research and Development Authority.
One of the ways in which these companies and others are making inroads is by adopting continuous manufacturing, which involves sustained processing of raw ingredients and completion of medicines instead of manufacturing in smaller batches.
Continuous manufacturing can come with high upfront equipment costs. But it also increases yield while decreasing the waste of traditional batch manufacturing, which makes it more economically competitive.
That’s because in continuous manufacturing, testing occurs intermittently throughout more automated processes, allowing for substandard product to be removed before it’s completed.
“We’re not just creating advanced processes, we’re relooking at chemistry that hasn’t been looked at in decades,” Demeria said. “We can reduce needed steps exponentially.”
A Statewide Biopharma Boom
While the Richmond-Petersburg area may be the epicenter of biopharma activity and alignment, dots are being connected across Virginia.
Just down Interstate 64, contract manufacturer Afton Scientific recently announced a $200 million expansion to its Albemarle County facility. Specializing in much-needed sterile filling of small-batch commercial and clinical trial injectables, the company has found its niche with larger manufacturers that require a high-touch approach for specialized drugs.
Founded in Waynesboro in 1991, Afton expanded to the Charlottesville area in the early 2000s and then took the approach of “ground and pound, slow growth,” COO David Pereira said. The company also specializes in presterilized vials, a business line that began with a Johnson & Johnson partnership and then spiked during COVID-19 as drugmakers manufactured and tested potential vaccines.
With the recently announced expansion, Afton will triple its lab space, incorporate more automation, and position the company to handle the next tier of batch sizes.
“If you think you’re ahead, you’re probably two years behind,” Pereira said. “As we grow, the expansion is opening the door for a different set of clients.”
That also means Afton will need to significantly expand its workforce, hiring more engineers, chemists, and lab workers.
“We’re surrounded by young talent, smart people who want to get with a company like this and grow,” Pereira said, highlighting the company’s proximity to top universities — notably the University of Virginia (UVA) in nearby Charlottesville and James Madison University (JMU), an hour away in Harrisonburg — and community colleges.
We’re surrounded by young talent, smart people who want to get with a company like this and grow.
Pereira credited the substantial resources that both Albemarle County and Virginia are providing to build a pipeline for the necessary specialized labor.
“Everything we need is here” in Virginia, he said.
Pereira and Afton only need to look north to see how this next workforce development chapter could play out. When Virginia won a $1 billion expansion at Merck’s Rockingham County facility, which produces the company’s vaccine for the human papillomavirus (HPV), workforce development initiatives were a key piece of the attraction for the global science and technology company. What emerged was an approved allocation from the Virginia General Assembly to support talent and workforce initiatives led by neighboring JMU and Blue Ridge Community College (BRCC). Designed to establish a pipeline of biotech engineering and computer science talent that could fuel Merck’s future growth, it included:
-
Introduction of specialized curriculum with dedicated classes and staff
-
A robust internship program and boot camps with relevant on-site training
-
Youth biomanufacturing camps to maximize the pipeline’s reach into K-12 education
As a result of these and a number of additional initiatives, more than 100 JMU and BRCC graduates have already been hired by Merck. Elsewhere in Virginia, VCU launched the country’s first doctorate in pharmaceutical engineering in 2019.
Last year, Gov. Glenn Youngkin announced plans for a $96 million “Virginia Research Triangle” intended to foster collaboration in biotech, life sciences, and pharmaceutical manufacturing. The group initially included UVA, VCU, and Virginia Tech; Old Dominion University was added in 2024.
Elsewhere in Virginia, the Advanced Pharmaceutical Tech Hub in the Richmond-Petersburg region was designated as one of 31 inaugural tech hubs by the U.S. Department of Commerce’s Economic Development Administration. The recognition allows the region to vie for a piece of the $70 million pie of federal grants allocated to the tech hubs.
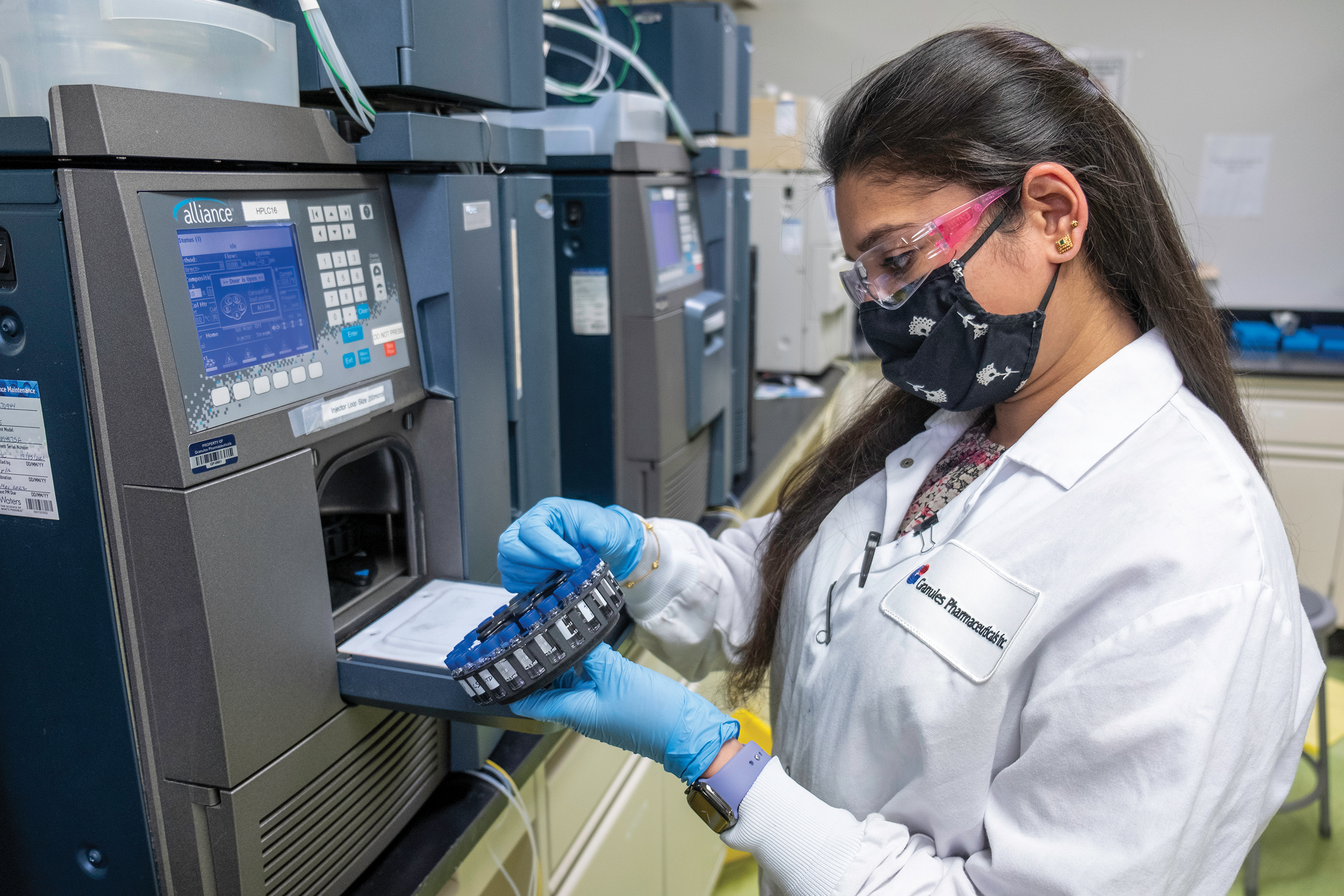
Granules Consumer Health, a division of Indian pharmaceutical company Granules India Ltd., specializes in the manufacturing of generic drug products including acetaminophen, ibuprofen, and other over-the-counter medications.
Building the Future of Biopharma
The Richmond-Petersburg cluster continues to grow. Civica is opening a 55,000-sq.-ft. laboratory testing facility in Chesterfield County’s Meadowville Technology Park. Meanwhile, Phlow and USP have completed neighboring labs in Richmond’s VA Bio+Tech Park — right beside M4ALL.
M4ALL is now working on 14 new global health projects, and will expand its already extensive capabilities to meet this new demand, thanks to an $18.7 million grant from the Bill & Melinda Gates Foundation.
Phlow’s Demeria is already issuing the call for more companies to join the Richmond-Petersburg area’s effort to create a fully connected supply chain.
“We’re going to need more than the original four,” he said.
Demeria points to recent events that dramatically affected the biopharma supply chain, from Baltimore’s Francis Scott Key Bridge collapse, to Hurricane Helene’s damage, to North Carolina’s Baxter International plant, which produces critical IV and sterile fluids.
“There’s no doubt that progress has been made, beginning with the transformative work underway in central Virginia,” Demeria said. “But disruptions to our essential medicines supply chain will persist, and it will take ongoing collaboration and tenacity to safeguard America’s medicine cabinet.”