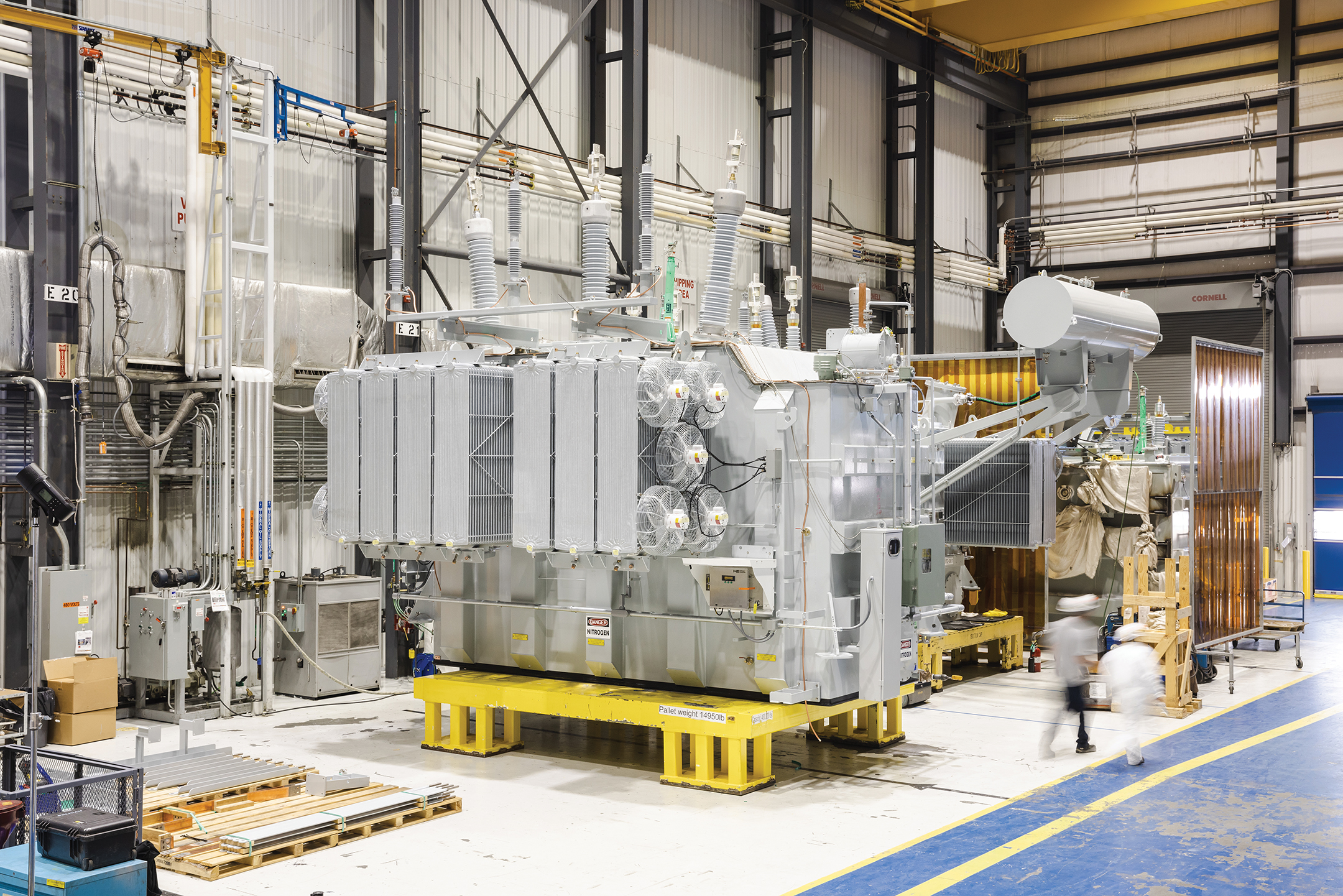
Hitachi Energy, Halifax County
It wasn’t until Clear toured a transformer plant that he recognized the incredible complexity manufacturers face in increasing supply. “I was amazed at the difficulty behind the manufacturing. These things are made by hand,” he said. “It appears to me that it is an industry where capacity is expensive to increase and could quickly lead to an oversupply situation if demand slows.”
Not anymore. The industry is preparing in a big way to match the demand they’re seeing today and, more importantly, the demand expected to continue. “We see this being a 7- to 10-year cycle, and possibly even longer,” McKinney said.
As a result, manufacturers across Virginia are working to increase supply of these essential components onshore to serve their customer base more effectively.
Hitachi Energy is working to match demand by expanding its facilities. Its Bland plant added capacity back in 2021, and now the company is adding 26,000 square feet to its South Boston facility. This will accommodate a new production line for manufacturing large transformers geared toward the utility and renewable energy markets. The addition comes with support from several state grants and is expected to create 165 new jobs.
Meanwhile, Delta Star, Inc., is expanding its 300,000-sq.-ft. East Coast manufacturing facility in Lynchburg by another 80,000 square feet. It’s the largest capital investment in the company’s more than 60 years of operations in Virginia.
Asa Keimig, media & PR manager for Delta Star, explained that the expansion will help the manufacturer maintain its reputation for industry-leading power solutions. The facility provides a diverse range of transformer sizes, as well as mobile transformers, to accommodate a span of market needs.