Site Selectors Seek Supply Chain Predictability
COVID-19 issues drove companies to rethink logistics operations
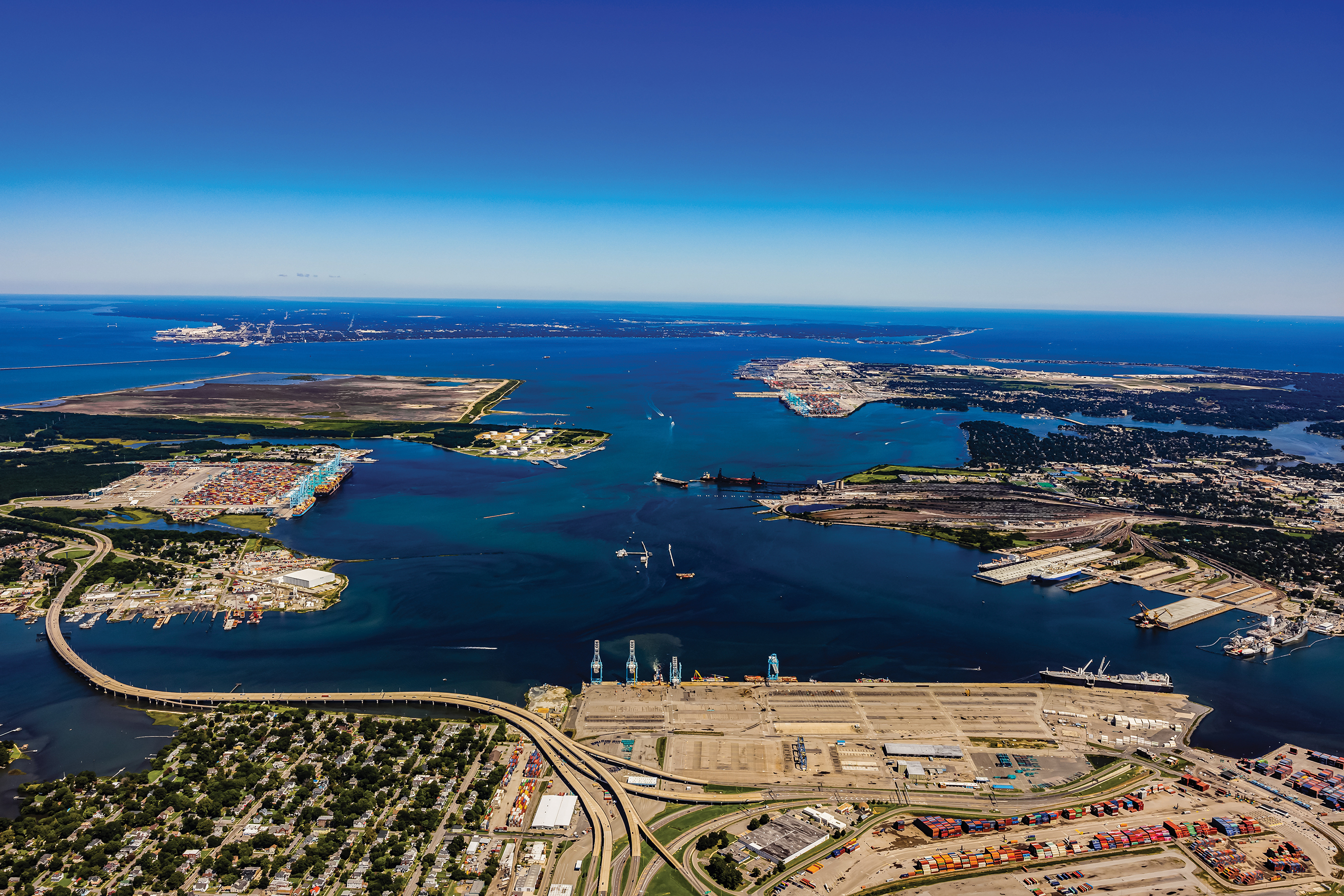
The Port of Virginia
Real estate developers have dealt with a daunting set of complications in the last few years, from increased borrowing costs to inflation to labor issues. It’s no surprise that developers and site selectors have focused on predictability as they consider supply chain factors in site decisions.
Supply chain predictability is paramount in every step as products travel from their point of origin to the end consumer, said Vincent Burke, senior managing director of development at Matan Companies, which is currently co-developing the Port 460 Logistics Center in Suffolk near The Port of Virginia’s Hampton Roads terminals.
That predictability, he said, must be in everything, “from the highway system to the rail system to the port to the technology used along the way.”
In a post-pandemic world, one thing is crystal clear: Supply chain considerations have emerged as an increasingly powerful driver of site selection. Sometimes it’s all about economies of scale. Sometimes it’s all about how a state responds to businesses’ needs. Sometimes it’s about companies hedging their supply chain bets by choosing more than one port to call home. In every case, however, it’s all about the relentless quest for predictability.
Location, Location, not Location
In an unpredictable supply chain world, location isn’t just about where a port is located — but where it’s not located. That’s because, Burke said, the global supply chain basically broke during the height of the pandemic. Many companies didn’t have enough built-in redundancies, nor were they flexible enough with their shipping and warehousing options. “The West Coast ports got choked and left folks scrambling to fix that,” Burke said.
During the height of the pandemic, warehouses at many West Coast ports were suddenly clogged with inventory as manufacturers and retailers worldwide found themselves facing an unpredictable virus. Last year’s negotiations for a new labor contract for 29 West Coast ports also complicated shipping decisions.
As a result, many companies are seeking more diversified port usage and shifting away from relying only on West Coast ports, according to Katie Lenss, managing director at New York-based developer Rockefeller Group. She said East Coast ports, such as The Port of Virginia, are benefiting from this new dynamic. The Port of Virginia grew container traffic by 32% between 2020 and 2022, ranking second only to Houston in growth rate.
Port Proximity Drives Supply Chain Investments
The main reason that Matan and Rockefeller partnered to develop the Suffolk site that will host the 540-acre Port 460 Logistics Center is its unique Virginia location, according to Burke. The port sits within a two-day drive of 75% of the entire U.S. population, making it an optimal location for logistics operations — particularly cold storage facilities that serve industries where freshness is paramount.
However, the operators of those facilities can’t rely on location alone to drive business. The average American warehouse is about 43 years old, according to CBRE research, and more than 80% of U.S. logistics assets were built before 2000. Many older warehouses were built under a now-adjusted set of best practices that has left owners to deal with lower-than-optimal ceilings, inefficient column spacing, and electricity issues.
Developers also want to operate in as pro-business an environment as possible. Companies are looking for certainty regarding permitting, utilities, and infrastructure. They also want to know how long it might take to get roads, rail, water, power, and sewer so they can confirm everything with their clients.
In addition to those issues, high interest rates and exacting federal regulations have challenged new development. As VEDP Vice President of Real Estate Solutions Michael Dreiling put it, “A major trend has been that the demands of the companies don’t match up with the interest rates and the time needed to deliver sites.”
“As interest rates go up, it’s more expensive to keep things in inventory,” said Devon Anders, president of the InterChange Group, which has 20 dry and cold storage industrial warehouses across Virginia. That’s why, he said, companies now need to be able to pivot quickly as an increasing number of geopolitical issues force quick decisions on exports and imports.
“We’re still seeing the impact of manufacturers trying to figure out what inventory they need to maintain,” Anders said. One effect of those adjustments, he said, has been unexpected partnership structures. As he put it, “There’s a lot more collaboration going on where distribution centers are located.”
Upgrades Make the Competitive Difference
Competing in such an environment requires states and port operators to be proactive with facility upgrades, and Virginia and its port are no exception. The port recently wrapped up $1.4 billion in upgrades to its Hampton Roads facilities, including a new, wider shipping channel that allows two-way traffic of ultra-large container vessels, cutting the amount of time such ships spend on berth by up to 15%.
Upgrading infrastructure isn’t the only way ports distinguish themselves. A swift, efficient customs process can help ports draw investment from foreign shippers that might otherwise look elsewhere.
“Infrastructure is hugely important — not only having quality infrastructure, but the ease of use,” said David MacNamara, a director in KPMG’s Site Selection and Project Development group. “Even if it’s more time on the boat, if you can clear your product quickly and spend fewer days in port, that can be a tipping point.”
Outside the port, the Virginia Department of Transportation (VDOT) is in the process of widening the current four-lane segments along a 10-mile stretch of Interstate 64 in Hampton and Norfolk and constructing new twin tunnels across Norfolk Harbor, doubling the road’s capacity.
“If the trucks leave the warehouse and get stuck in traffic, that doesn’t work,” Burke said.
The global supply chain management market exceeded $27 billion in 2022 and is projected to exceed $76 billion by 2032, according to Valuates Reports projections. That helps explain why localities are focused on showing why they rank among the top places to store and ship products. In the end, decisions often come down to which state or locality can be the most predictable.