Making Shipping Easier for Manufacturers
Multimodal focus helps Virginia facilities create value for companies
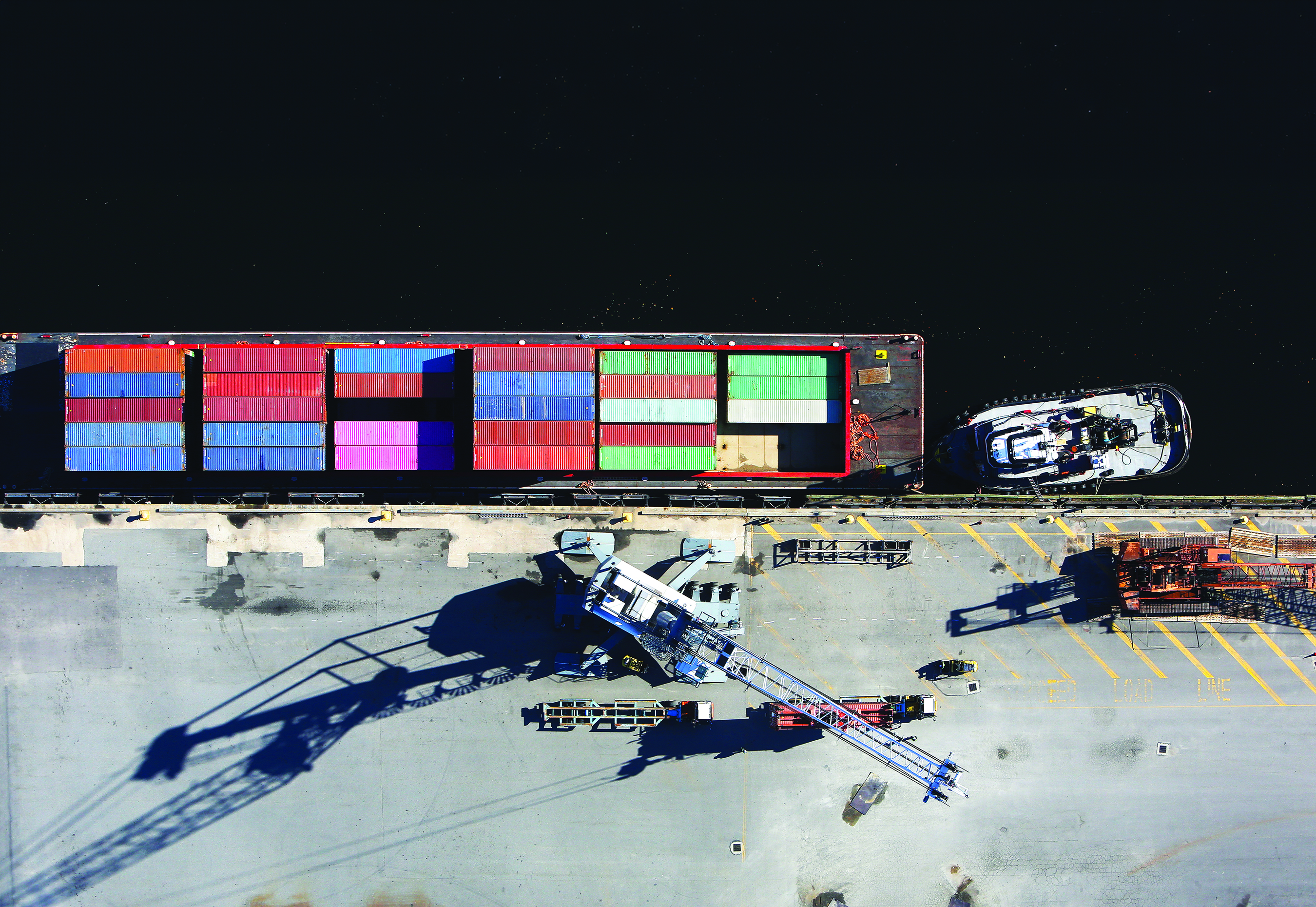
Richmond Marine Terminal
Supplier and customer accessibility has always played a key role in industrial site selection decisions. But the supply chain shakeups over the last five years have pushed manufacturers to rethink the types of sites that might allow them to best serve their key stakeholders. In the face of global pandemics and conflicts, tariffs and inflationary pressure, natural disasters and extreme weather events — running alongside consumer demands for greater personalization and faster deliveries — companies are looking for sites with infrastructure in place to help them pivot when transportation challenges arise.
“Given the challenges posed by the COVID-19 pandemic and ongoing geopolitical conflicts, the logistics industry has become increasingly demanding,” said Julian Amato, director of business development for Kuehne+Nagel, a global logistics provider with nearly 1,300 locations in more than 100 countries. “Customers no longer wish to spend hours waiting on hold for a customer service representative. Instead, they seek localized expertise within their own time zone to provide tailored advice.”
This perspective has driven many global companies to open locations near key Virginia logistics hubs. Kuehne+Nagel’s Virginia locations reflect this focus — its Northern Virginia office is adjacent to Washington Dulles International Airport. Amato works out of Richmond, where the port’s Richmond Marine Terminal (RMT) helps companies move product along the James River via barge. The company’s Virginia locations provide versatile, multimodal access to customers and suppliers along the East Coast.
“In this high-demand industry, everyone relies on carriers, freight forwarders, or other logistics service providers,” Amato said. “Having a local presence and providing shippers with an expert to consult are absolutely crucial.”
Local Benefits, Global Reach
Facilities like RMT — currently undergoing a $6.1 million upgrade to allow faster processing for trucks and extended hours for barge loading and unloading — provide non-vessel operating common carriers like Kuehne+Nagel options for moving goods. This redundancy is proving essential for ensuring speed to market, even in the face of unexpected events. Both of the Virginia Port Authority’s inland terminals, RMT and the Virginia Inland Port (VIP) in Warren County, are convenient to multiple interstate highways, supplemented by on-site rail service at VIP and the barge service at RMT.
Virginia has also seen an uptick in construction for distribution centers and warehousing, adding to local manufacturers’ supply chain efficiency. For Cascades Containerboard Packaging’s Bear Island plant in Ashland, a new three-year contract with several distribution centers across Virginia is a key step that will allow the company to have a more stable raw material supply, according to Jim France, the plant’s logistics director.
Cascades Inc., a Canadian producer of green packaging and paper tissue products, acquired its lightweight recycled containerboard operation in the former Bear Island Paper Mill in 2018. The site was selected in large part due to a location that brought Cascades closer to a number of key suppliers. This new distribution agreement now makes it easier for the plant to manage inventory provided by those suppliers.
Upon announcing the site selection decision in 2018, the company noted that the Ashland plant’s geographic positioning would enable Cascades to increase its competitiveness and provide customers a more diversified product offering. France confirmed that has proven true, because the company has been able to expand its recycled linerboard products to include a range of lighter-weight materials as a result of new supplier relationships. While Cascades works to lower packaging weight for a variety of reasons, RMT’s intermodal rail capabilities — the facility offers direct rail service via CSX and connects to Norfolk Southern’s network via a local switch — have proven advantageous in shipping heavy commodities like paperboard across long distances.
“There are many suppliers within the Mid-Atlantic region, and our location has allowed us to secure several local supplier contracts,” France said. “Most of these suppliers are located along the Interstate 95-Interstate 64 corridor.”
On the customer side, that centralized location also allows the company to more easily reach customers from New York to Georgia. The plant’s reach also extends to the Midwest, as well as Mexico and South America. From the interstates to rail and barge service at RMT, Virginia offers companies like Cascades access to a complete multimodal gateway, and the company’s location in the Richmond-Petersburg area allows it to utilize all modes of transport to move its products on to the rest of the country and the world.
Richmond
Simplified Logistics Eliminate Headaches
While Kuehne+Nagel has maintained a presence at Dulles for several years supporting unique needs related to humanitarian aid, government shipping, and broader aerospace logistics, the company recently expanded its footprint. In 2022, the company strategically opened a central Virginia location to better serve clients who were previously assisted by representatives in Baltimore or the Carolinas.
For Kuehne+Nagel, establishing a Richmond office goes beyond mere shipping efficiency — it’s about empowering customers to comprehend and navigate their choices, Amato said. The Port of Virginia’s owner-operator model inherently simplifies logistics, when compared to other ports that lease terminals to various operators.
“Regardless of the terminal, whether it’s the inland port or barge service, we know exactly who to contact,” Amato said. “This clarity reinforces customers’ understanding that the infrastructure is readily available, offering comparable reach, if not quicker and more efficient service.”
Rather than focusing solely on streamlining shipping processes, Kuehne+Nagel’s Richmond office aims to provide on-the-ground expertise, guiding customers and global colleagues toward Virginia-based solutions for shipping, warehousing, and other critical logistics requirements.
To provide that local touch, companies need to do more than simply open an office — they must actively engage with stakeholders operating local transportation infrastructure. Amato and his team have achieved this by participating in local associations, fostering relationships, and gaining insights into the logistics landscape.
Joining these networks has also connected Amato’s team to a wealth of resources that help shippers and other stakeholders within Virginia’s logistics and transportation network navigate international trade.
As The Port of Virginia and nearby localities continue investing in infrastructure enhancements, collaborative efforts between businesses and local governments demonstrate their commitment to success and customer satisfaction.
“Being in proximity to our customers isn’t just about geography; it’s about forging meaningful connections,” Amato said. “These connections are the bedrock of our strategy, allowing us to build trust, understand customer needs, and deliver exceptional experiences.”