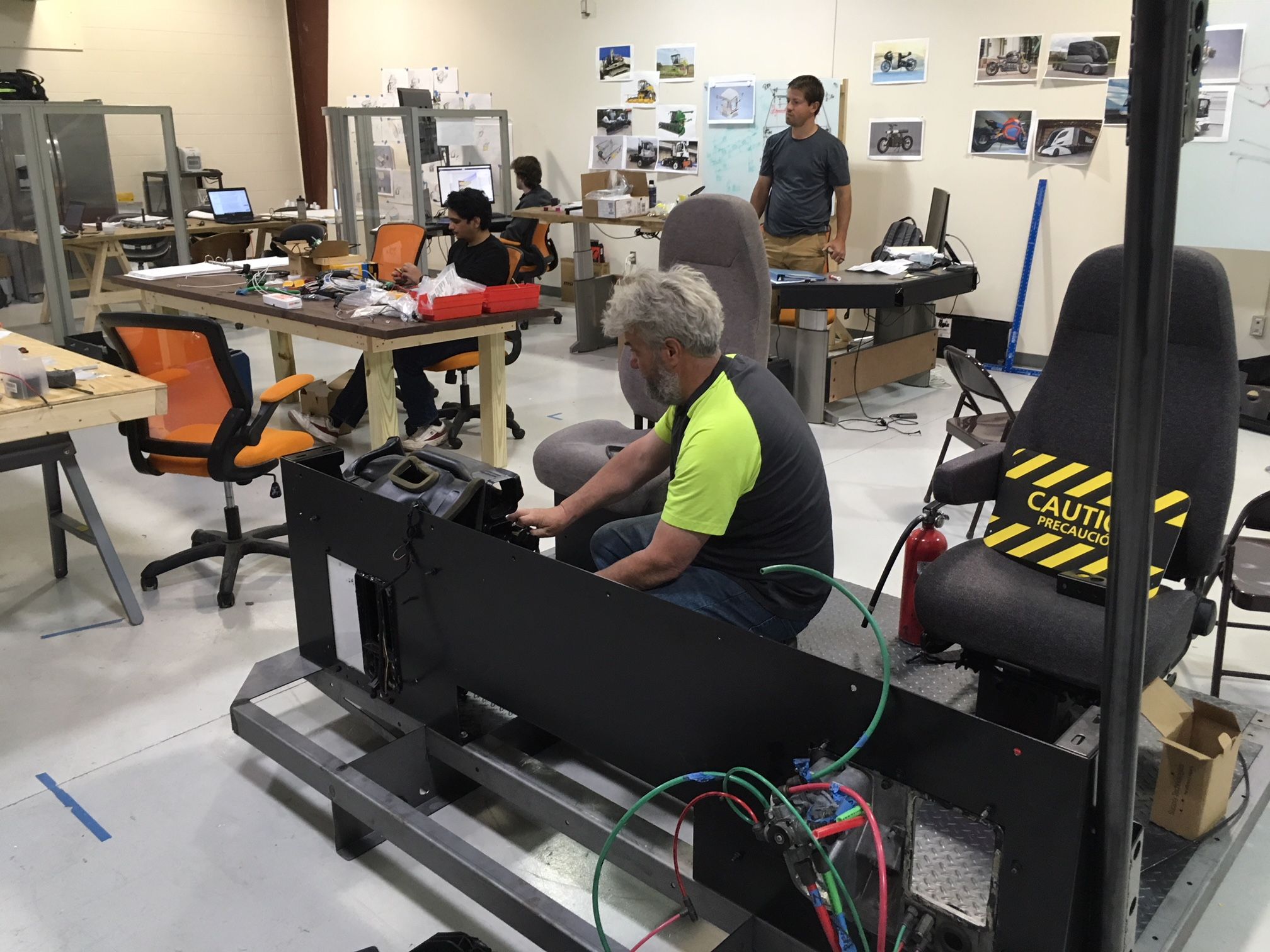
Trova Commercial Vehicles, Pulaski County
Modern cars and trucks are constructed from parts from numerous suppliers, each with their own proprietary hardware and software components that all produce data in different formats. The challenges of accessing and interacting with this data limit its utility in making improvements to the driving experience.
Amazon Web Services (AWS), with multiple offices and data centers in Northern Virginia, is one of the companies trying to improve the way users interact with data from connected vehicles. Late last year, AWS announced an agreement with BlackBerry QNX to develop BlackBerry IVY, a cloud-connected software platform that will allow auto manufacturers to more effectively collect and analyze that data. Then-AWS CEO Andy Jassy, now CEO of Amazon, said the technology would enable manufacturers to “transform vehicles from fixed pieces of technology into systems that can grow and adapt with a user’s needs and preferences.”
The AWS/BlackBerry partnership is just one example of major companies partnering to push connected-vehicle technology forward. General Motors is working with Microsoft to accelerate the commercialization of unmanned vehicles, while Volkswagen, with its U.S. headquarters in Fairfax County, and Bosch are using Microsoft Azure to build cloud-based vehicle platforms.
Safer Work Zones for Drivers and Workers
Just some of the research into connected-vehicle applications involves what’s happening inside the vehicle. The Virginia Tech Transportation Institute (VTTI) is developing numerous technologies in partnership with the Virginia Department of Transportation (VDOT), including a mapping application, active safety vests, and autonomous attentuator vehicles to improve work-zone safety for drivers and road workers alike.
“We have a philosophy that automated vehicles and connected vehicles will both be safer if they’re communicating with each other and with the infrastructure,” said Mike Mollenhauer, director of VTTI’s Division of Technology Implementation.
The first step is a tablet-based mapping application called “Work Zone Builder,” which allows VDOT managers to use a tablet to designate an area on a map showing exactly where upcoming road work will be and what type of work will be done.
The app then imports all relevant rules from a work-area protection manual to determine optimal placement of signs, traffic cones, and other features, and populates the map with these details to guide crews in setting up the work zone. That data is also packaged into a format that can be retrieved by a connected vehicle to warn drivers about upcoming hazards and reduced speed limits.
VTTI is also developing a “Smart Work Zone System” to protect workers by communicating data on individual workers’ locations to vehicles approaching a work zone. Workers wear a vest with an integrated GPS-enabled radio that connects to a mesh network, pinpointing the workers in the zone down to 20 centimeters of accuracy. The communication goes both ways — the vests are equipped with numerous systems to alert workers to approaching vehicles, with reminders given in visual (LED lights), aural (shoulder-mounted speakers), and haptic (vibrating pulses) form.
Individual workers are not the only crew in danger in a work zone. Drivers of the slow-paced truck-mounted attentuator vehicles that typically follow and protect workers and vehicles in moving work zones are at risk, too. VTTI is working on getting drivers out of those vehicles entirely through an autonomous truck-mounted attentuator (ATMA) vehicle that automatically convoys with the work vehicles it follows at a preset distance. The system has demonstrated following consistency to within 20 centimeters of a lead vehicle, and VTTI is preparing to take an ATMA prototype onto the roads for testing in early 2022.
VTTI is tackling the development and testing of these systems in stages, starting with less complex, limited-access highway environments. The first steps, while incremental, have the potential to make crucial road improvements safer for drivers and workers alike.
“If we can even get it out and operating in a limited domain, that’s a step forward,” Mollenhauer said.