Brick by Brick
The LEGO Group Builds a Sustainable Future in Virginia

The LEGO Group rendering, Chesterfield County
The LEGO Group’s new manufacturing facility in Chesterfield County is designed to support the company’s sustainability ambitions. From building practices to construction materials to operating functions to landscaping, the LEGO Group’s only U.S. manufacturing facility is poised to be a showcase of sustainable practices and design when it opens in 2027.
“What we plan to do, and it’s part of our LEGO ambition, is to first reduce the amount of energy that our buildings need,” said Cecilia Fernandez, LEGO’s Virginia-based sustainability construction manager. “So we try to make our production lines and our buildings run in a much more efficient way. What we can’t reduce, we compensate for with renewable energy.”
The site will be the sixth international manufacturing facility for the Danish toy company. “The U.S. is a growing market for the LEGO Group,” Fernandez said. With the new facility, “We can produce closer to where we’re actually selling the products. We see it as a win-win.”
The company plans to invest more than $1 billion to construct the carbon-neutral plant in Meadowville Technology Park. The 1.7-million-sq.-ft. precision manufacturing facility will be powered by its own solar farm and create more than 1,760 new jobs for the Greater Richmond area.
Sustainability Key to the Virginia Solution
Virginia’s commitment to renewable energy and sustainability was a major factor in the LEGO Group’s selection of the Meadowville site. As CEO Niels B. Christiansen said at the announcement, “We were impressed with all Virginia has to offer, from access to a skilled workforce, support for high-quality manufacturers, and great transport links. We appreciate support for our ambition to build a carbon-neutral-run facility.”
Sustainability begins with construction. Concrete, steel, glass, drywall — all of the material selections will focus on lowering the carbon footprint, such as by using recycled content whenever possible, Fernandez said. In addition, the entire office building, where site administrators will work, will be made from engineered mass timber — thick, compressed layers of wood that match the high-strength ratings of concrete and steel, but are lighter weight and significantly less carbon-intensive than those materials.
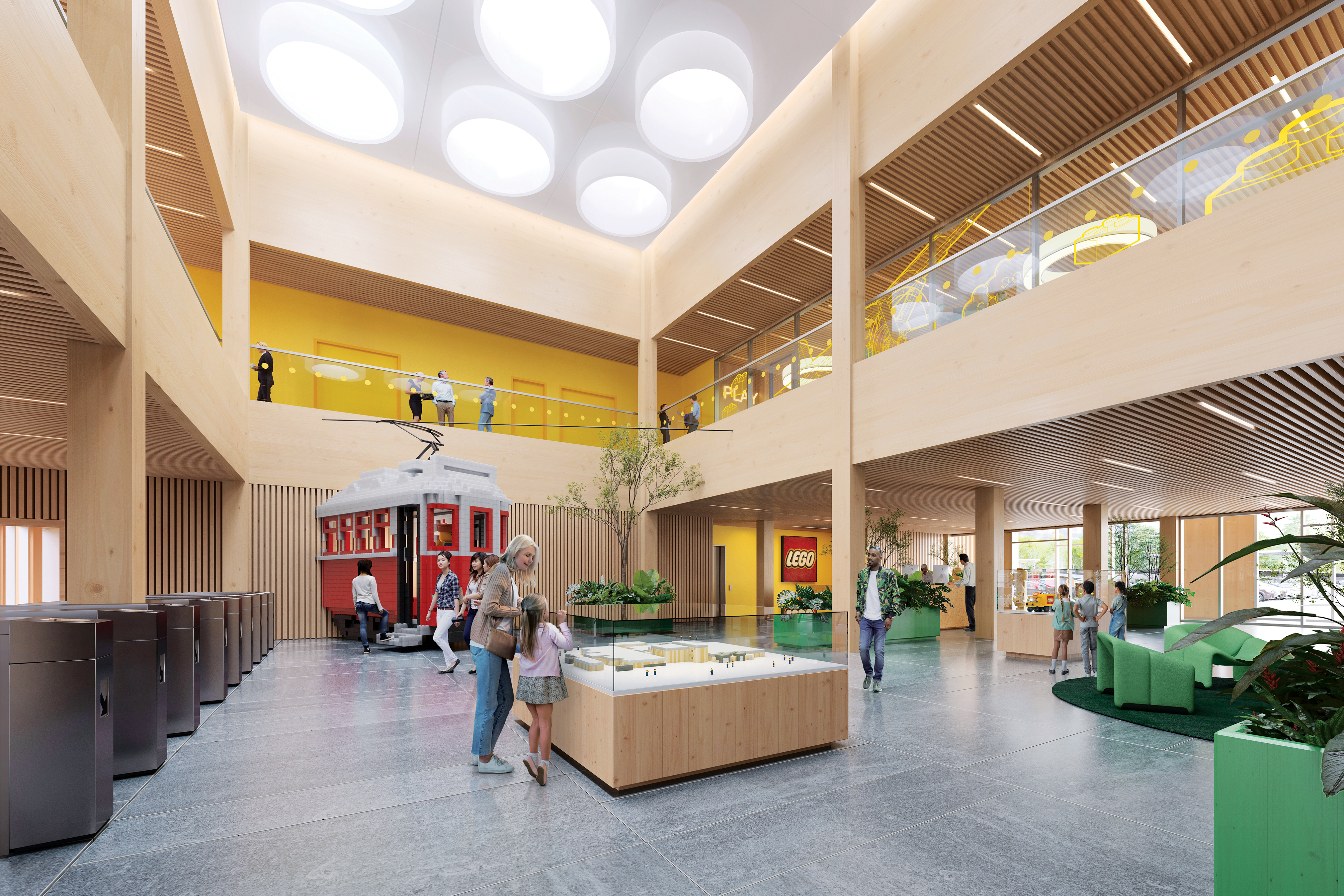
The LEGO Group rendering, Chesterfield County
“Our early calculations show that we can save up to 40% of the carbon embedded in the building by using mass timber versus using ordinary concrete or steel,” Fernandez said.
The company plans to use wood from areas close to Virginia in the mass timber, from species native to the area. The wood will also be certified by the Forest Stewardship Council, which confirms that the wood was harvested sustainably in a way that protects fragile ecosystems, respects native cultures and economies, and does not decimate forests.
A Different Kind of Business Climate
The buildings will be constructed for optimum energy efficiency, with increased insulation to retain heat in the winter and cool air in the summer, and automated building monitoring systems to control temperature and report electricity usage. Sensors will be able to detect when a room is empty and will subsequently switch off lights and adjust heating and cooling systems where it’s possible to do so and not interfere with manufacturing processes.
“We want to make sure we’re not just blasting heating or cooling everywhere in the building even though the building is empty,” Fernandez said. Similarly, “Why have rooms lit up when there’s no one on the entire floor?”
Monitors in the factory will also track humidity levels, which is critical for LEGO’s new packaging materials. After years of packing LEGO bricks in plastic bags, the company has committed to phasing out single-use plastic packaging. At the Richmond plant, this means producing paper-based bags to hold the play bricks. But these materials are delicate and vulnerable to humidity changes, Fernandez said, so the company will install monitors to make sure certain buildings maintain an optimum humidity at all times.
The Solar Solution
The entire facility will be powered by an on-site solar plant comprising as many as 40,000 ground panels and 20,000 roof panels, covering an area of 85 acres, for a total capacity of 30–35 megawatts, Fernandez said.
The LEGO Group is aiming for the highest green-building certification possible — at least LEED Gold, hopefully LEED Platinum. LEED, or Leadership in Energy and Environmental Design, is a certification that companies or builders can apply to receive for their projects. LEED projects are rated on how effectively they reduce their contribution to climate change, enhance human health, impact water resources, affect biodiversity, relate to the green economy, and affect community and natural resources.
LEED Platinum status is a lofty goal for manufacturing operations like the LEGO Group’s because the certification is designed primarily for office or residential buildings, Fernandez said. For instance, projects get points for having more windows, or being able to easily adjust the temperature, but neither are possible in the factory.
The company is also looking to secure WELL certification — which assesses the health and wellness of people who work at the plant — for the project. This means features like a central staircase that entices employees to take the stairs rather than use an elevator, lots of indoor plants to foster employee well-being, and healthy food offerings.
Sustainability and wellness don’t stop at the facility door. The LEGO Group plans to install landscaping that protects and restores the natural habitat. The facility is designed to be water-neutral, meaning that rainwater falling on the site will be captured as much as possible and used for everything except human consumption, to include toilet flushing, irrigation, cleaning, and humidification inside the buildings. The production facility also aims to send zero waste to the landfill by partnering with various sub-suppliers who can either use or properly dispose of the waste.
To build a sustainable workforce, the company engaged the Virginia Talent Accelerator Program, a workforce initiative created by VEDP in collaboration with higher education partners. The program is designed to accelerate new facility startups through direct delivery of recruitment and training services fully customized to a company’s unique products, processes, equipment, standards, and culture. Last year, Business Facilities named the program the No. 1 customized workforce training program in the nation.
The first Talent Accelerator service delivered to the LEGO Group, a customized recruitment website that went live with the project announcement, drew more than 3,000 job candidates within 36 hours. Since then, the Talent Accelerator team has produced recruiting and training videos, screened candidates, and delivered more than 2,600 hours of job-specific training for the LEGO Group’s initial hires. This support, delivered in collaboration with Brightpoint Community College and the Community College Workforce Alliance, will continue through the opening of the permanent facility.
With the main facility under construction, the company currently employs about 200 people at a temporary packing facility in nearby Colonial Heights. That facility opened in November. When the main plant comes online in 2027, the people now at the temporary facility will transfer over to the permanent location.
“They’re starting to learn about the LEGO culture and values,” Fernandez said. “And they will actually then be the ones who will model and share those values to new employees at the permanent facility.”